03 Jan Pepperidge Farm Tour
Johtaja edelleen
Pepperidge Farm jatkaa investointeja uusimpaan robotiikkaan ja muihin huippuluokan järjestelmiin tuotannon tehokkuuden, kapasiteetin ja joustavuuden lisäämiseksi lippulaivallaan Denverissä, Pa..,
By Dan Malovany

Kun Denverin, Pa:ssa sijaitseva tehdas aloitti toimintansa vuonna 1991, Pepperidge Farmin uusimmalla pelaajalla oli kaikki laitteet, jotta se voisi olla all-star-toiminta tulevina vuosina. Denverin tehdas, joka rakennettiin 611 000 neliöjalkaa lähes ennennäkemättömän kalliilla 180 miljoonalla dollarilla, oli seitsemän vuotta rakennusvaiheessa, ja se oli tekniikan alku, joka sisälsi aikansa kattavimmat tietokoneintegroidut valmistusominaisuudet (CIM).
Kuten mikä tahansa tulokas, myös Denverin tuotantolaitos tarvitsi kuitenkin pientä harjoittelua, ennen kuin se pystyi näyttämään potentiaalinsa kunnolla. Ensimmäiset askeleet kohti suuren luokan menestystä edellyttivät työntekijöiden kouluttamista uusiin tietokoneisiin ja automaatioon ja sen jälkeen sellaisen toimintarakenteen luomista, jonka avulla työntekijät pystyivät hyödyntämään tätä teknologiaa. Aluksi yli puolet työntekijöistä tuli Denverin korvaamasta ikääntyneestä Downingtownin leipomosta, joka sijaitsi 34 mailia Pennsylvanian Turnpiken varrella. Vaikka monilla näistä työntekijöistä oli arvokasta käytännön leipomiskokemusta, he tarvitsivat lähes yhtä paljon koulutusta kuin monet niistä uusista työntekijöistä, jotka Pepperidge Farm palkkasi lopulta kadulta, kun tehdas pääsi vauhtiin 90-luvun puolivälissä.
Se johtui siitä, että Denverin huipputekniset laitteet tekivät siitä yhden uusista leipomoista, joissa suorituskyky määräytyy vähemmän leipomiskokemuksen kuin ohjelmoitavan ohjauksen ymmärtämisen ja tilastollisen valvonnan noudattamisen perusteella. Parantaakseen tehtaan suorituskykyä vuosien mittaan Denverin tiimin on täytynyt kehittää uusia järjestelmiä, jotka eivät ainoastaan nostaneet työntekijöiden oppimiskäyrää, vaan vaativat myös täysin uudenlaista ajattelua tuotantokapasiteetin ja linjojen tehokkuuden parantamiseksi.
Tehtaan tilastollisista prosessinohjauksista kerättyjen tietojen avulla kunkin linjan tiimit kokoontuvat viikoittain analysoimaan tapoja, joilla voidaan pienentää hävikkiä, lisätä tuotannon tasaisuutta, minimoida vaihtotyöt, tehostaa läpimenokykyä, vähentää uusien tuotteiden käynnistysongelmia tai parantaa turvallisuutta. Joissain tapauksissa prosessin uudelleenajattelu merkitsi hienosäätöä siellä täällä, kuten sen toteaminen, että Milano-uunin kaistan tasaisuus oli kriittinen tekijä tasaisen soikeiden voileipäkeksien tuottamisessa. Toisissa tapauksissa tällainen uudelleenajattelu on pakottanut Pepperidge Farmin kyseenalaistamaan sen tavan, jolla se perinteisesti valmistaa myydyimpiä kuvakkeitaan, kun yhtiö on jatkanut investointeja uuteen kehittyvään teknologiaan.
”Tiedämme, että kun teknologia muuttuu, meidän on muututtava teknologian mukana”, Denverin tehtaanjohtaja Dean Moll toteaa. ”Kun tämä tehdas rakennettiin, olimme hyvin valmistautuneet 90-luvulle. Joka päivä varmistamme, että olemme valmistautuneet 2000-lukuun. Uskon, että olemme. Vain kolmen viime vuoden aikana olemme esimerkiksi kaksinkertaistaneet kahden keskeisen linjan – Goldfishin ja Milanon – läpimenon.”
Denverin tehdas on tämän vuoden B&CMA:n teknisen konferenssin esittelykierros. Nykyään laitos on jaettu kahteen toiminta-alueeseen – 351 000 neliöjalan alue keksien tuotantoa varten ja 260 000 neliöjalkaa leivän ja sämpylöiden tuotantoa varten. Laitoksessa on kaiken kaikkiaan 12 linjaa, mukaan lukien kolme leipomolinjaa, joilla valmistetaan viipaloituja leipiä, ranskanleipiä ja sämpylöitä. Yhdeksällä keksilinjalla valmistetaan Goldfish-keksejä sekä erilaisia korkealaatuisia keksejä Soft Baked- ja Chocolate Collections -kekseistä Milanoihin, Brysselin kekseihin ja muihin.
Mollin mainitsemat Goldfish-linja 7:n ja Milano-linja 3:n parannukset ovat klassisia esimerkkejä siitä, miten Pepperidge Farm on muuttanut Denverin tehtaan insinööritieteellisestä virstanpylväästä, jossa teknologia kontrolloi ihmisiä, laitokseksi, jossa ihmiset ovat nyt koneiden yläpuolella.
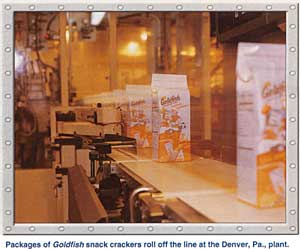
Aiemmin Goldfish-prosessia olisi ollut kerettiläistä edes harkita peukaloimista. Nykyään tehtaalla on kuitenkin käytössä radiotaajuuskuivauslaitteisto, joka on kaksinkertaistanut linjan läpimenon. Aiemmin Pepperidge Farm ei voinut lisätä uunin läpimenoaikaa merkittävästi Goldfish-linjalla, koska se olisi lisännyt merkittävästi kosteuden määrää lopputuotteessa, mikä vaikutti keksin rakenteeseen. Koska kuivauslaite vähentää välipalakeksien kosteuden puoleen vaikuttamatta väriin, kokoon tai muihin leivontaominaisuuksiin, tehdas pystyy kaksinkertaistamaan tuotantokapasiteettinsa ilman uutta uunia tai uutta Goldfish-linjaa. Se on myös antanut Pepperidgelle mahdollisuuden valmistaa erilaisia uusia linjalaajennuksia, kuten jättimäisiä Goldfish-keksejä, joiden kosteuspitoisuus on korkeampi.
”Tämä on esimerkki teknologiasta, jota ei ollut olemassa, kun tehdas rakennettiin”, Moll toteaa. Kaiken kaikkiaan hän lisää: ”Kyse ei ole siitä, mitä tekisimme toisin, jos tehdas rakennettaisiin tänään. Kyse on siitä, miten teknologia on muuttunut ja miten me olemme muuttuneet sen mukana.”
Pepperidge Farm on lisäksi lisännyt Goldfish-linjaan maustekeksejä, jotka muistuttavat perunalaivatehtaissa käytettäviä maustekeksejä, makupuhallettuja välipalakeksejä varten. Vastatakseen vuosien varrella kasvaneeseen markkinointitarpeiden määrään Team Goldfish suunnitteli kuljettimien labyrintin, joka johtaa linjoilta useille pakkausasemille miltä tahansa linjalta.
Pepperidge voi valmistaa kaleidoskooppi Goldfish-pakkauskokoonpanoja 1 unssin kerta-annoksesta tai tavallisista 6 unssin pusseista makupuhallettuihin maitotölkkeihin, 31 unssin ruokatarjoilupakkauksiin tai 38 unssin klubimyymälöiden pakkauskokoon.”
Milano linjalla tuotantolaitos muutti tapaa, jolla se laskee taikinaerotettaan. Aikaisemmin yrityksellä oli kaksi taikinaerottelijaa – toinen varajärjestelmänä, jos toinen tarvitsi puhdistusta tai jos se hajosi. Hidastamalla tallettajien nopeuksia ja synkronoimalla ne insinöörit ovat lisänneet läpimenoa 50 prosenttia ilman, että on tarvinnut lisätä toista laitetta, toteaa insinööripäällikkö Paul Brooker.
”Jos toinen tallettajista menee rikki, voimme silti ajaa linjaa yhdellä tallettajalla ja nostaa tuotantoa samoilla nopeuksilla kuin ennenkin”, Brooker sanoo. ”Se antaa meille todella joustavuutta. Voimme käyttää kahta tallentajaa maksimoidaksemme kapasiteetin tai voimme käyttää niitä varajärjestelmänä, jos jokin menee pieleen. Nämä ovat pieniä asioita, jotka auttavat parantamaan tuottoa.”
Nopeampien tallentimien ansiosta Denver siirtyi vuonna 1998 asentamaan nopeamman, toisen sukupolven robottijärjestelmän, joka poimii ja sijoittaa keksejä 1320 keksiä minuutissa, kun vanhempi järjestelmä, joka asennettiin alun perin vuonna 1988, oli 880 keksiä minuutissa.
Uuden järjestelmän 12 robottikäsivartta pystyvät poimimaan ja sijoittamaan 120 keksiä minuutissa, mikä on lähes kaksinkertainen nopeus verrattuna ”vanhaan” robottijärjestelmään, jossa on 20 käsivartta, jotka työskentelevät 60-75 keksiä minuutissa. Brookerin mukaan uusi järjestelmä on nopeampi, koska neljän servolaitteen ansiosta se on suunniteltu kevyille hyötykuormille nopeammilla syklinopeuksilla, kun taas vanhempi järjestelmä oli suunniteltu raskaammille hyötykuormille ja hitaammille syklinopeuksille autojen ja muiden raskaiden koneiden kokoonpanoa varten.
Koska robotiikka on kehittyneempää, taitavampaa ja yhä edullisempaa, takaisinmaksuaika on lyhentynyt, sanoo Dave Watson, Pepperidgen yritystekniikan johtaja, joka oli johtava insinööri ja yksi tärkeimmistä arkkitehdeistä Denverin tehtaan käynnistämisessä kymmenen vuotta sitten.
Watson huomauttaa, että ensimmäisen sukupolven robottijärjestelmä maksoi 3,5 miljoonaa Yhdysvaltain dollaria, se toi 1,1 miljoonan dollarin vuotuiset säästöt välittömässä työvoimassa ja työntekijän työkorvauskustannuksissa, ja sen takaisinmaksuaika on 3,9 vuotta. Se on 20,2 prosentin sisäinen korkokanta (IRR). Uusi järjestelmä maksoi 2,0 miljoonaa dollaria, tuotti 1,3 miljoonan dollarin vuotuiset säästöt vain suorassa työvoimakustannuksissa, ja sen takaisinmaksuaika on 1,5 vuotta eli sisäinen korkotuotto on 41,3 prosenttia, Watson lisää.
Kapasiteetin lisääntyminen on saanut Pepperidge Farmin perustelemaan edelleen investointia prototyyppiin, robotisoituun keksien kuppausjärjestelmään, joka poimii yksittäisiä keksejä liikkuvalta hihnalta ja lataa ne paperikupeilla useissa eri suunnissa nopeudella 120 kuppia minuutissa.
”Ilman tätä robotiikkaa linjastolle ei voisi laittaa tarpeeksi väkeä, jotta se pysyisi tuotantonopeuden mukana”, Brooker sanoo. ”Ennen kuin saavutimme nämä nopeudet ja omistimme tämän linjan , emme voineet perustella investointeja, jotka teimme siihen. Meidän on käytettävä tätä joka työvuorossa”, mikä on tällä hetkellä 15 työvuoroa viikossa.
Juuri tänä kesänä käyttöön otetussa järjestelmässä on kaksi robottikuppia, jotka kumpikin poimivat ja sijoittavat 660 keksiä – tai 100 pussia – minuutissa. Järjestelmä maksoi 3,2 miljoonaa dollaria, tuo 1,2 miljoonan dollarin vuotuiset säästöt pelkästään välittömässä työvoimassa, ja sen takaisinmaksuaika on 3,26 vuotta eli IRR on 27,8 %.
Automaation parannusten ansiosta Denverin laitos on pystynyt kokoamaan tilastojen osalta urakointikauden: koko laitoksen tuotekoteloiden määrä nousi tänä vuonna 26 % yli 12 miljoonaan.
Se on lähes 60 % enemmän kuin vuonna 1997 tuotetut 7 miljoonaa tuotelaatikkoa ja kolminkertainen määrä verrattuna ensimmäisen täyden toimintavuoden aikana vuonna 1992 tuotettuun määrään.
Samanaikaisesti tehdas on vähentänyt jätemääräänsä 50 %, mikä on säästänyt yritykselle miljoonia dollareita. Ei siis ole yllättävää kuulla, että Denver voitti MVP-palkintoa vastaavan palkinnon, kun tiimi sai Pepperidgen perustajan mukaan nimetyn Margaret Rudkin -palkinnon vuoden tehtaana.
”Olimme onnekkaita saadessamme aloittaa ensiluokkaisena tuotantolaitoksena, ja olemme vuosien mittaan investoineet pitääkseen laitoksen huipputasolla”, sanoo Moll, joka huomauttaa Denverin saaneen ISO 9002 -sertifikaatin tänä vuonna. ”Haluamme pitää sen huippulaitoksena, mutta se on huippuluokkaa ja huippuluokkaa vain, jos työntekijämme vievät meidät sinne.”
Pepperidge Farmin kasvua on viime vuosina vauhdittanut yhtiön siirtyminen ikonistrategiaan, jossa yhtiö laittaa markkinointivoimansa portfolionsa suurimpien ja parhaiden tuotteiden, kuten Goldfish-, Milano ja Swirl-leipien, taakse. Kun näiden tuotteiden myyntiä lisätään, tuotantolinjojen volyymit kasvavat, mikä parantaa tuotannon tehokkuutta. Samalla osa tehokkuuden parantamisesta säästyneistä rahoista ohjataan markkinointiin ja T&K-ohjelmiin, joilla luodaan uusia pakkauksia, kasvatetaan mainosbudjetteja tai tuodaan markkinoille uusia tuotteita, kuten menestyksekkäästi debytoineet suklaakuorrutteiset Milanot, joita valmistetaan kausiluonteisesti myöhemmin tänä vuonna.
Tuotanto on tyypillisesti käynnissä 24 tuntia vuorokaudessa viidestä seitsemään päivänä viikossa. Irtojauhot varastoidaan 10:een 120 000 kilon siiloon. Sokeria säilytetään kahdessa 120 000 kilon siilossa. Jauhot siirretään 20 000 paunan käyttösäiliöihin tarkan skaalauksen ja nopeampien kierrosaikojen varmistamiseksi. Laitoksessa on 50 000 paunan säiliöt rasvalle, maissisiirapille, rypsiöljylle, sekoitetulle öljylle ja 80 000 paunan suklaasäiliö. Kuudessa käsin täytettävässä säiliössä säilytetään pieniä ainesosia, kuten ruisjauhoja, tärkkelystä ja vehnägluteenia. Mikroainekset mitataan käsin ja laitetaan sitten kärryihin, joihin kuhunkin mahtuu yksi erä.
Välipohjatasolla Denverin CIM-järjestelmän valvontahuone näyttää Houston Controlilta, jossa keskusvalvontatietokoneet valvovat yli 100:n kuituoptisilla linjoilla yhdistetyn, teollisuuskäyttöön soveltuvan tietokoneen verkkoa. Jokaisella linjalla on oma valvontatietokoneensa, samoin ainesosien käsittelyssä ja sekoituksessa. Pepperidge Farm on korvannut alkuperäiset IBM 386 PC/2 -tietokoneet IBM 486 -tietokoneilla, joissa käytetään yleisesti saatavilla olevia ohjelmistoja ja laitteistoja, ei patentoituja, mikä tekee päivittämisestä edullisempaa.
Välipohjatasolla keksien puolella viisi 1 300 kilon keksisekoitinta ja kaksi 1 500 kilon keksisekoitinta valvovat reseptuuria ja sekoitusaikaa. Kaikissa on CO2-järjestelmät taikinan lämpötilan säätöä varten. Sekoittamisen jälkeen erät putoavat 20-jalkaisten kourujen läpi, jotka nostetaan lattiassa olevien rakojen läpi ensimmäiselle tasolle.
Kuudessa keksilinjassa kolme tuottaa suklaalla päällystettyjä tai kuorrutettuja keksejä. Muut tuottavat pehmeäleivottuja, pikkuleipäkeksejä, lajitelmapakkauksia tai erilaisia suklaalastuja ja muita rautalankakeksejä. Linja 1 valmistaa myös Goldfish Graham-välipaloja. Keksilinjojen uunien koot vaihtelevat 150-300 ft:n välillä.
Ainutlaatuisimpia ovat ehkä Milano-linjat. Siellä keksit kulkevat meikkauksen jälkeen 150-jalkaisen uunin läpi 60-jalkaiseen jäähdytystunneliin. Oikeanlaisen jäähdytyksen varmistamiseksi Pepperidge käytti uunin ”myyriä” muistuttavaa laitetta mittaamaan tunnelin lämpötilaa, ilman nopeutta ja muita muuttujia. Kun minipohjaaja on levittänyt appelsiini-, minttu- tai suklaakuorrutteen, Milanot kulkevat robotisoituihin sandwich-järjestelmiin. Tuplasuklaatäytteiset Milanot päällystetään vielä toisella pohjustajalla ennen sandwichausta. Koska niissä on kaksinkertainen määrä täytettä, tuplasuklaatäytteiset Milanot jäähdytetään toisen kerran, jotta varmistetaan, että tuote on tiivis.
Seuraavaksi Milanot juoksevat kohti robottikuppia 1320 kuppia minuutissa. Vastavirtaperiaatteella viisi keksiä kerrallaan suunnataan etummaiseen järjestelmään, kun taas kuusi kuppia kerrallaan puristetaan takimmaisesta järjestelmästä. Yksi valokuvasilmä varmistaa, että kupit on puristettu, kun taas toinen varmistaa, että keksi on oikein päällystetty. Jos se näkee tummaa suklaata, kuten täytteessä, eikä valkoista vaniljaa, kuten keksissä, järjestelmä olettaa, että keksiä ei ole leivottu. Kaiken kaikkiaan järjestelmä on ohjelmoitu täyttämään kupit. Jos keksejä ei poimita, ne kuljetetaan loppuun ja kierrätetään myöhemmin tai hävitetään.
Täytön jälkeen täytetyt kupit kiertävät 180°:n kierroksen täyttäjille, jotka asettavat ne pussiin, jotka suljetaan, koteloidaan ja lähetetään varastoon.
Goldfish-linjalla juuri sekoitettu, hiivalla kasvatettu taikina saa pidennetyn käymisen ennen kuin se kaadetaan välipohjatasolta ensimmäiseen kerrokseen, jossa se laminoidaan, leikataan ja leivotaan. Kuljettuaan radiotaajuuskuivaimen läpi, joka puolittaa tuotteen kosteuden oikealle tasolleen, Goldfishit kulkevat maustekuivaimen ja uuden suuremman kokoisen akkumulaattorin läpi, joka asennettiin, kun linjan kapasiteetti kaksinkertaistettiin.
Akummulaattorista Goldfishit kulkevat kauhakuljettimiin yhteen monista skaalauslaitteista, jotka sijoittavat täsmälleen tuotteen painon mukaisen määrän alla olevaan pakkaukseen. Sulkemisen jälkeen täytetyt Goldfish-pussit kulkevat yksitellen laatikkopakkaajille.
Linjalla kehittyneet anturit valvovat tarkasti väriä, kosteutta, korkeutta ja öljyn tai suolan määrää. Laadunvarmistushenkilöstö ottaa rutiininomaisesti näytteitä linjalta pisteytystä ja testausta varten.
Laajassa varastossa työntekijät purkavat tuotteet kuljettimilta varastoalueittain. Joka päivä Denverissä täytetään noin 40 traktoriperävaunua, ja Denverin keksitoiminta palvelee 120:tä Keski-Atlantin ja Uuden-Englannin varikkoa. Tyypillisesti varastossa on viikon varasto keksejä ja keksejä.
Vaihdon virtaviivaistaminen on kaksi osa-aluetta, joita yritys pyrkii parantamaan keksipuolella. Aiemmin Denverissä tehtiin vaihtotyöt jokaisen 8 tunnin työvuoron jälkeen. Nyt tehdas tekee niitä keskellä vuoroa, ”jotta varastomme pienenisi lähes olemattomiin”, Moll sanoo.
”Opimme leipomopuolelta, miten vaihtoja tehdään lennossa”, Moll selittää. ”Tavoitteenamme on siirtää tämä ajatteluprosessi keksipuolelle.”
Uusi tuotekehitys on toinen alue, jolla Pepperidge Farm ja sen Denverin tehdas pyrkivät virtaviivaistamaan toimintaansa. Aiemmin uuden tuotteen käyttöönotto kesti yleensä 4-6 kuukautta. Uudessa ”Project Lightening” -nimisessä ohjelmassa yritys haluaa päästä ideasta tuotantoon kahdessa kuukaudessa.
Tällaiset haasteet kustannusten alentamiseksi, laadun parantamiseksi, läpimenon tehostamiseksi ja turvallisuuden lisäämiseksi sekä ISO 9002 -sertifioinnin 20 tiukkaa standardia ovat saaneet Mollin järjestämään tehtaan hallintorakenteen uudelleen. Nykyään Denverissä on kolme tuotepäällikköä – yksi leipomo-, keksi- ja keksejä varten – jotka raportoivat tuotantopäällikkö William Livingstonelle. Saapuvien ainesosien ja lähtevien tuotteiden valvomiseksi suunnittelu-, vastaanotto-, varastointi- ja lähetyspäälliköt raportoivat toimitusketjupäällikkö Stephen Liebille.
”Osasyynä järjestelmällisiin muutoksiin, joita olemme tehneet, on yrityksen kasvu vuosien varrella”, Moll sanoo. ”Ja koska jouduimme tuomaan uusia työntekijöitä, tarvitsemme vahvan järjestelmän, jonka avulla voimme tuottaa johdonmukaisesti tuotteita, jotka vastaavat yhtiömme standardeja.”
Kysyttäessä, mitä hän tekisi toisin, jos hänellä olisi mahdollisuus rakentaa Denverin tuotantolaitos uudelleen tyhjästä, Moll vastaa: ”En usko, että kyse on siitä, mitä olisimme tehneet eri tavalla. Teimme hyvää työtä. Se on hieno tehdas. Tehtävämme on – teknologian muuttuessa – parantaa sitä, mitä meillä on täällä, ja tehdä siitä vielä parempi.”
Tällaisen toimeksiannon turvin voidaan sanoa, että Pepperidge Farmille ”ei ole koskaan tavallista päivää” Denverissä, Pa:ssa.
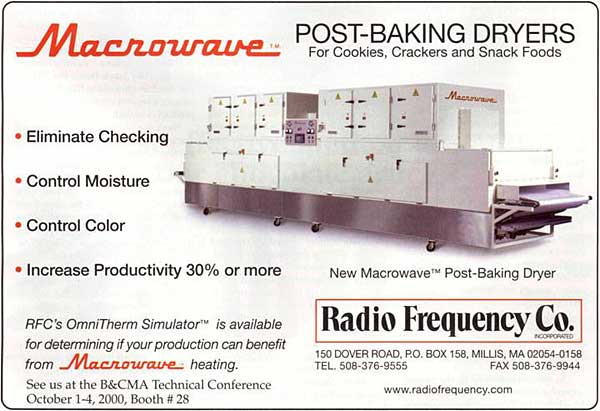
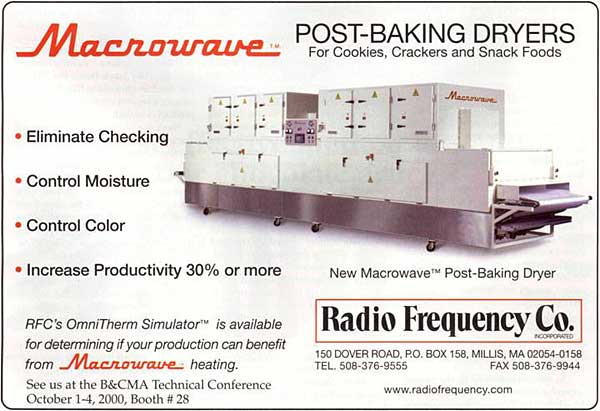