03 Jan Pepperidge Farm Tour
Still the leader
Pepperidge Farmは、ペンシルバニア州デンバーの旗艦工場において、生産効率、生産能力、柔軟性を高めるために最新のロボットやその他の最先端システムへの投資を続けています。
By Dan Malovany

1991年にデンバー、ペパリッジ・ファームの工場がスタートしたとき、登録された最新のペパリッジ・ファームのプレーヤーには、今後何年にもわたってオールスターとなれるようなすべての設備が整っていました。 611,000 平方フィート、1 億 8,000 万ドルという前代未聞のコストで建設されたデンバー工場は、7 年の歳月をかけ、当時最も包括的でコンピュータ統合製造 (CIM) の機能を組み込んだ技術のスタート地点でした。
しかしながら、他のルーキー同様、デンバー工場はその潜在能力を本当に発揮するまで少し調教を必要としました。 大リーグでの成功への第一歩は、新しいコンピューターとオートメーションについて従業員を訓練し、その技術を従業員が活用できるようなオペレーション構造を作ることであった。 当初、従業員の半数以上は、ペンシルベニア・ターンパイクを34マイル(約16キロメートル)行ったところにある、ダウニングタウンにある老舗のベーカリーから移ってきた人たちだった。 これらの従業員の多くは貴重な実地での製パン経験を持っていましたが、90年代半ばに工場が軌道に乗るにつれ、ペパリッジ・ファームが最終的に外部から雇用した多くの従業員と同じくらい多くのトレーニングを必要としました
それは、デンバーの最新機器が、製パン経験よりもプログラム制御を理解し統計制御に従うことによってパフォーマンスが決まる新種のベーカリーのひとつであったためです。 工場のパフォーマンスを長年にわたって向上させるために、デンバーのチームは新しいシステムを考案しなければなりませんでした。それは、従業員の学習曲線を引き上げるだけでなく、生産能力とライン効率を向上させるために、既成概念にとらわれない考え方を必要としました。
工場の統計プロセス制御から集めたデータを使用して、各ラインのチームは毎週会議を開き、ロスの削減、生産の安定性の向上、切り替えの最小化、スループットの向上、新製品の立ち上げ問題の削減、安全性の向上について分析を行っています。 例えば、ミラノオーブンのバンドの平坦度が、楕円形のサンドイッチクッキーを安定的に生産するための重要な要素であることを突き止めるなど、工程の見直しがあちこちで行われています。
「技術が変われば、我々も技術とともに変わらなければならないことは分かっています」と、デンバーの工場長、Dean Mollは指摘します。 「この工場が建設されたとき、私たちは90年代に向けて十分に準備を整えていたのです。 この工場ができた時、私たちは90年代に対応することができた。そして、毎日、2000年代に対応できるように準備をしている。 そう思っている。 たとえば、この3年間で、ゴールドフィッシュとミラノの2つの主要ラインの処理能力を2倍にしました」
デンバー工場は、今年のB&CMA技術会議の注目ツアーとなっています。 現在、この施設は、ビスケット製造用の351,000平方フィートのエリアと、パンとロールパン製造用の260,000平方フィートのエリアの2つのオペレーションエリアに分けられています。 工場全体では、スライスパン、フランスパン(ストリングライン)、ロールパンを製造する3つのベーカリーラインを含む12のラインがあります。 9つのビスケットラインでは、ゴールドフィッシュクラッカーや、ソフトベイクド、チョコレートコレクション、ミラノ、ブリュッセルなど、さまざまな高級クッキーを製造しています。
Moll 氏が言及した Goldfish ライン 7 と Milano ライン 3 の改善は、ペパリッジ ファームがデンバー工場を、テクノロジーが人間をコントロールするエンジニアリングのマイルストーンから、機械より人間である施設に変えた典型例と言えます。 しかし現在では、工場では高周波乾燥装置を使用し、ラインの処理能力を 2 倍にしました。 以前は、Pepperidge FarmはGoldfishラインのオーブンの処理能力を大幅に上げることができませんでした。最終製品の水分量が大幅に増加し、クラッカーの食感に影響が出るからです。 乾燥機はスナッククラッカーの水分を半分に減らし、色やサイズ、その他の焼成特性には影響を与えないため、工場では新しいオーブンやGoldfishラインの増設をすることなく生産能力を2倍にすることができます。 また、Pepperidge 社は、水分レベルを高めた巨大な Goldfish クラッカーなど、さまざまな新しいライン拡張を生産できるようになりました。
「これは工場建設時にはなかった技術の一例です」と Moll は指摘します。 全体として、「もしこの工場が今日建設されたら、私たちは違ったことをするだろうか、という質問ではありません。 1438>
さらに、ペパリッジ・ファームはゴールドフィッシュのラインで、味付けしたスナック・クラッカーにポテト船工場で使用されるものと同様のシーズナーを追加しました。
Pepperidge は、1 オンスのシングルサーブや標準的な 6 オンスの袋から、フレーバーブラスト加工のミルクカートン、31 オンスのフードサービスまたは 38 オンスのクラブストア サイズまで、万華鏡のようにさまざまなゴールドフィッシュ パッケージ構成を製造することが可能です。 以前は、2台のデポジッターを使用していました。1台は、もう1台がクリーニングを必要とする場合や故障した場合のバックアップとして使用していました。 デポジッターの速度を遅くし、同期させることにより、エンジニアは、別の装置を追加することなく、処理能力を 50% 向上させました。 とBrooker氏は言います。「本当に柔軟性があります。 2台のデポジッターを使用して生産能力を最大化することもできますし、何か問題が発生したときのバックアップとして使用することもできます。 デポジッターの速度が向上したことで、1998年にデンバーは、より高速の第2世代ロボット・クッキー・サンドイッチ・システムの導入に踏み切りました。
新システムの12本のロボットアームは、1分間に120個の速度でピッキングと配置が可能で、1分間に60~75個の速度で作業する20本のアームを持つ「古い」ロボットシステムのほぼ2倍の速度に達します。 旧システムが自動車や重機の組み立てなど、より重いペイロードとより遅いサイクル速度向けに設計されていたのに対し、新システムは4つのサーボ装置で、より速いサイクル速度で軽いペイロードを扱うように設計されているからだとBrookerは述べています。
ロボット工学はより洗練され、より巧みになり、ますます安価になっているため、投資回収期間は短くなっていると、10 年前のデンバー工場の立ち上げで主任エンジニアであり主要設計者の 1 人だった Pepperidge の企業エンジニアリング担当ディレクター Dave Watson 氏は述べています。 これは内部収益率(IRR)20.2%に相当します。 新システムのコストは200万ドル、直接労働コストのみで年間130万ドルの節約となり、キャッシュバックは1.5年、IRRは41.3%であるとWatsonは付け加えています。
生産能力の向上により、Pepperidge Farm は、移動ベルトから個々のクッキーをピックアップし、1 分間に 120 カップの速度で複数の方向から紙カップにセットする、ロボットによるクッキー カッピング システムのプロトタイプへの投資をさらに正当化するように促されました。 「このスピードに到達し、このラインを専用にするまでは、私たちがこのラインに行った投資を正当化することはできませんでした。
今年の夏に稼働したばかりのこのシステムは、2台のロボットカッパーを備え、それぞれが1分間に660個のクッキー(または100袋)をピック&プレースします。 このシステムのコストは 320 万ドルで、直接労働のみで 120 万ドルの年間節約を実現し、キャッシュ バックは 3.26 年、IRR は 27.8% です。
オートメーションの改善により、デンバーの施設は、工場全体の製品のケース数が 26% 増加して今年は 1200 万を超え、統計的に見てもキャリア シーズンとなっています。
これは 1997 年に生産された 700 万ケースより 60% 近く多く、1992 年の操業初年度の生産量の 3 倍です。
同時に、この工場では廃棄物を 50% 減らし、会社を数百万ドル節約しています。 Moll 氏は、デンバー工場が今年 ISO 9002 認証を取得したことに触れ、「私たちは幸運にも一流の施設としてスタートし、長年にわたって最先端を維持するために投資してきました」と語ります。 「
ここ数年のペパリッジ・ファームの成長の原動力は、ゴールドフィッシュ、ミラノ、スワールなどの最大かつ最高の製品にマーケティング力を注ぐ、アイコン戦略への転換にあります。 これらの製品の売上を伸ばすことで、生産量も増え、生産効率も向上する。 一方、効率化によって節約された資金の一部は、マーケティングおよび研究開発プログラムに投入され、新しいパッケージの作成、広告予算の増加、あるいは今年後半に季節限定で生産されるチョコレート入りのミラノの成功例のような新商品の展開に使われています
生産は通常、1日24時間、週5~7日稼働しています。 バルクの小麦粉は10基の12万ポンドのサイロに貯蔵されています。 2つの12万ポンドのサイロには砂糖が貯蔵されています。 小麦粉は、正確な計量と迅速なサイクルタイムを確保するため、20,000ポンドの使用ビンに移されます。 ショートニング、コーンシロップ、キャノーラ油、ブレンド油用の50,000ポンドのタンクと80,000ポンドのチョコレート用タンクがあります。 ライ麦粉、でんぷん、小麦グルテンなどの副原料は、手作業で充填された6つのビンに収納されています。
中2階のデンバーのCIMシステムの制御室は、中央の監視コンピュータが光ファイバー回線で結ばれた100台以上の産業用高性能PCのネットワークを監督するヒューストンコントロールのような場所である。 各ラインには、原料の取り扱いやミキシングと同様に、それぞれのスーパーバイザーコンピューターがある。 ペパリッジ・ファームは、初期のIBM 386s PC/2をIBM 486sに置き換えました。これは、独占的ではなく、一般に入手可能なソフトウェアとハードウェアを使用しており、アップグレードをより手頃なものにします。
ビスケット側の中二階では、5台の1,300ポンドのクッキーミキサーと2台の1,500ポンドのクラッカーミキサーが処方と混合時間を制御しています。 すべて生地の温度をコントロールするCO2システムを搭載しています。 ミキシング後、バッチは20フィートのシュートを通って落ち、床のスロットを通って1階まで吊り上げられる。
6つのクッキーラインでは、3つのラインでチョコレートボトムコートまたはエンローベッドクッキーが生産されている。 その他はソフトベイク、ショートブレッド、アソートパック、チョコレートチップやその他のワイヤーカットクッキーなどを生産しています。 ライン1では、Goldfishのグラハムスナックも生産しています。
おそらく最もユニークなのはミラノラインであろう。 そこでは、クッキーは製造後、150フィートのオーブンを通り、60フィートの冷却トンネルに移動する。 適切な冷却を確保するため、Pepperidgeはオーブンの「モグラ」に似た装置を使い、トンネルの温度、風速、その他の変数を測定しています。 ミニボトマーがオレンジ、ミント、チョコレートなどのコーティングを施した後、Milanosはロボットサンドウィッチングシステムに運ばれる。 チョコレートが2つ入ったMilanosは、サンドする前に2番目のボトマーによってもう1度コーティングされる。
次に、ミラノは1分間に1,320個の割合でロボットカッパーに向かって走ります。 カウンターフロー方式で、一度に5個のクッキーが前方のシステムへ、一度に6個のカップが後方のシステムから排出されます。 1つのフォトアイがカップの脱脂を確認し、もう1つのフォトアイがクッキーのトッピングを確認する。 もし、フィリングのダークチョコレートとクッキーのホワイトバニラが一致しない場合、クッキーはサンドされていないと判断されます。 全体として、システムはカップに充填するようにプログラムされています。
充填後、充填されたカップは180度回転してスタッファーに送られ、スタッファーはそれらを袋に入れ、密封し、ケースに入れて倉庫に送ります。
金魚のラインでは、イーストで育てられた新鮮な混合生地は、中2階から1階へ捨てられる前に長時間発酵を受け、そこでラミネート、型抜き、焼成が行われる。 高周波乾燥機で製品の水分を半分に減らし、適切なレベルにした後、金魚はシーズナー、そしてラインの生産能力を2倍にしたときに設置された、より大きなサイズのアキュムレーターを通過する。 密封された金魚の袋は、一列になってケース詰めされます。
ライン上では、高性能のセンサーが色、水分、高さ、油や塩の量を入念に監視しています。
広大な倉庫では、従業員がコンベアからデポごとに製品を分解しています。 毎日、約40台のトラクタートレーラーがデンバーに運び込まれ、同社のビスケット事業は大西洋中部とニューイングランドの120のデポにサービスを提供しています。 通常、この倉庫には1週間分のクッキーやクラッカーの在庫がある。
ビスケット側で改善しようとしているのは、段取り替えの効率化の2点です。 以前は、デンバーは8時間のシフトごとにチェンジオーバーを行っていました。 今は、「在庫をゼロにするために」シフトの途中で切り替えています。
「私たちはベーカリー側から、その場で変更する方法を学んでいます」と Moll は説明します。 「私たちの目標は、その思考プロセスをビスケット側に持ち込むことです。」
新製品開発は、ペパリッジ・ファームとそのデンバー工場が合理化に努めているもう 1 つの分野です。 以前は、新製品を導入するのに通常4~6ヶ月かかっていました。
コスト削減、品質向上、スループットの改善、安全性の向上といった課題に加え、ISO 9002 認証の 20 の厳しい基準が、Moll に工場の管理構造の再編成を促しました。 現在、デンバー工場では、ベーカリー、クッキー、クラッカーの3つのプロダクトマネージャーが、オペレーションマネージャーのウィリアム・リビングストーンのもとで生産を監督している。 原材料の入荷と製品の出荷を監督するため、計画、入荷、倉庫、出荷の各マネージャーは、サプライチェーンマネージャーのスティーブ・リーブに報告します。
「私たちが行った組織的変化の理由の一部は、長年にわたる会社の成長にあります」と、モルは言います。 「そして、新しい人材を迎え入れなければならなかったため、当社の基準に見合う製品を一貫して生産するための強力なシステムが必要になりました」
デンバーの施設をもう一度ゼロから作り直すチャンスがあれば、違ったことをするかと問われたモールは、次のように答えました。 私たちは良い仕事をした。 素晴らしい工場だ。 私たちの使命は、技術の変化に応じて、ここにあるものを改良し、より良いものにすることです」
このような使命があるので、ペパリッジ・ファームにとって、ペンシルベニア州デンバーに「普通の日がない」と言ってもよいでしょう
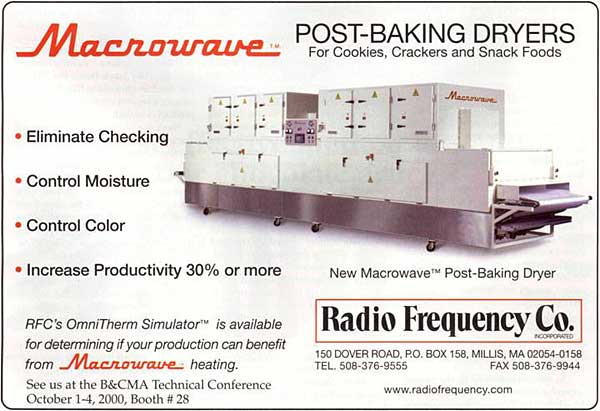