03 ian Pepperidge Farm Tour
Încă lider
Pepperidge Farm continuă să investească în cele mai noi sisteme robotizate și alte sisteme de ultimă generație pentru a spori eficiența, capacitatea și flexibilitatea producției la nava sa emblematică din Denver, Pa.., fabrica.
De Dan Malovany

Când fabrica din Denver, Pennsylvania, a început să funcționeze în 1991, cel mai nou jucător Pepperidge Farm de pe listă avea toate echipamentele necesare pentru a fi o operațiune de top pentru anii următori. Construită pe o suprafață de 611.000 de metri pătrați la un cost aproape nemaiîntâlnit de 180 de milioane de dolari, fabrica din Denver a fost construită timp de șapte ani și a fost un început de tehnologie care a încorporat cele mai cuprinzătoare capacități de fabricație integrată pe calculator (CIM) din vremea sa.
Cu toate acestea, ca orice începător, fabrica din Denver a avut nevoie de puțină experiență înainte de a-și putea arăta cu adevărat potențialul. Primii pași spre succesul din liga mare au implicat instruirea angajaților cu privire la noile computere și automatizări, apoi crearea unei structuri operaționale care să le permită lucrătorilor săi să valorifice această tehnologie. Inițial, mai mult de jumătate dintre angajați au venit de la brutăria îmbătrânită din Downingtown, Pennsylvania, pe care Denver o înlocuise și care se afla la 34 de mile mai jos pe Pennsylvania Turnpike. În timp ce mulți dintre acești angajați aveau o experiență valoroasă și practică de coacere, ei au avut nevoie de aproape la fel de multă pregătire ca mulți dintre angajații suplimentari pe care Pepperidge Farm i-a angajat în cele din urmă de pe stradă, pe măsură ce fabrica a luat avânt la mijlocul anilor ’90.
Aceasta pentru că echipamentele de ultimă generație de la Denver au făcut ca aceasta să facă parte din noua rasă de brutării în care performanța este determinată mai puțin de experiența de coacere și mai mult de înțelegerea controalelor programabile și de respectarea controalelor statistice. Pentru a îmbunătăți performanța fabricii de-a lungul anilor, echipa din Denver a trebuit să conceapă noi sisteme care nu numai că au ridicat curba de învățare a forței de muncă, dar au necesitat, de asemenea, o gândire total ieșită din comun pentru a îmbunătăți capacitatea de producție, precum și eficiența liniei.
Utilizând datele adunate din controalele statistice ale procesului fabricii, echipele de pe fiecare linie se întâlnesc săptămânal pentru a analiza modalitățile de reducere a pierderilor, de creștere a consistenței producției, de minimizare a schimbărilor, de îmbunătățire a randamentului, de reducere a problemelor de pornire a noilor produse sau de îmbunătățire a siguranței. În unele cazuri, o astfel de regândire a procesului a implicat o modificare ici și colo, cum ar fi determinarea faptului că planeitatea benzii de pe cuptorul Milano a fost un factor critic în producerea de fursecuri sandwich ovale constante. În alte cazuri, o astfel de regândire a forțat Pepperidge Farm să pună în discuție modul în care produce în mod tradițional cele mai bine vândute icoane ale sale, pe măsură ce compania a continuat să investească în noile tehnologii emergente.
„Știm că, pe măsură ce tehnologia se schimbă, trebuie să ne schimbăm odată cu ea”, remarcă Dean Moll, directorul fabricii din Denver. „Când a fost construită această fabrică, eram bine poziționați pentru anii ’90. În fiecare zi, ne asigurăm că suntem pregătiți pentru anii 2000. Cred că suntem. Doar în ultimii trei ani, de exemplu, am dublat producția pe două linii cheie – Goldfish și Milano.”
Fabrica din Denver este turul prezentat în cadrul Conferinței tehnice B&CMA din acest an. În prezent, instalația este împărțită în două zone de operațiuni – o zonă de 351.000 de metri pătrați pentru producția de biscuiți și 260.000 de metri pătrați pentru producția de pâine și rulouri. În total, fabrica are 12 linii, inclusiv trei linii de panificație care produc pâine feliată, pâine franțuzească (string line) și rulouri. Cele nouă linii de biscuiți produc biscuiți Goldfish, precum și o varietate de fursecuri premium, de la Soft Baked și Chocolate Collections la Milanos, Brussels și altele.
Ambunătățirile de pe linia 7 Goldfish și linia 3 Milano la care se referă Moll sunt exemple clasice despre modul în care Pepperidge Farm a transformat fabrica din Denver dintr-o piatră de hotar inginerească în care tehnologia controla oamenii într-o instalație în care acum oamenii sunt mai presus de mașini.
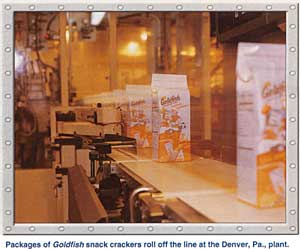
Anterior, ar fi fost eretic să se ia în considerare chiar și modificarea procesului Goldfish. Astăzi, însă, fabrica folosește un echipament de uscare prin radiofrecvență care a dublat randamentul liniei. În trecut, Pepperidge Farm nu putea crește dramatic randamentul cuptorului pe linia Goldfish, deoarece ar fi crescut semnificativ cantitatea de umiditate din produsul final, ceea ce ar fi afectat textura biscuiților. Deoarece uscătorul reduce la jumătate umiditatea biscuiților pentru gustări, fără a afecta culoarea, dimensiunea sau alte caracteristici de coacere, fabrica este capabilă să dubleze capacitatea de producție fără a fi nevoită să instaleze un nou cuptor sau o linie Goldfish suplimentară. De asemenea, a permis companiei Pepperidge să producă o varietate de noi extensii de linie, cum ar fi biscuiții giganți Goldfish, care au un nivel de umiditate mai ridicat.
„Acesta este un exemplu de tehnologie care nu exista atunci când a fost construită fabrica”, notează Moll. În general, adaugă el, „nu este vorba despre ce am face diferit dacă fabrica ar fi fost construită astăzi. Este vorba despre modul în care tehnologia s-a schimbat și cum ne-am schimbat odată cu ea.”
Mai mult, la linia Goldfish, Pepperidge Farm a adăugat condimente, care sunt similare celor folosite în fabricile de nave de cartofi, pentru biscuiții săi de gustări cu aromă. Pentru a satisface numărul tot mai mare de nevoi de marketing de-a lungul anilor, echipa Goldfish a proiectat un labirint de benzi transportoare care duc de la linii la mai multe stații de ambalare din orice linie.
Pepperidge poate produce un caleidoscop de configurații de ambalaje Goldfish, de la pungi de 1 oz. pentru o singură porție sau pungi standard de 6 oz. până la cutii de lapte sablate cu arome, de 31 oz. pentru servicii de alimentație publică sau de 38 oz. pentru magazine de tip club.
Pepperidge poate produce un caleidoscop de configurații de ambalaje Goldfish, de la 1 oz. pentru o singură porție sau pungi standard de 6 oz. până la cutii de lapte sablate cu arome, de 31 oz. pentru servicii de alimentație publică sau de 38 oz. pentru magazine de tip club.
Pe linia Milano, fabrica a schimbat modul în care depune aluatul. Anterior, compania avea două depunătoare – una ca rezervă în cazul în care cealaltă avea nevoie de curățare sau se defecta. Prin încetinirea vitezelor de depunere și sincronizarea acestora, inginerii au crescut producția cu 50% fără a adăuga o altă piesă de echipament, notează Paul Brooker, managerul departamentului de inginerie.
„Dacă unul dintre depunători se defectează, putem în continuare să rulăm linia cu un singur depunător și să ridicăm producția la viteze ca înainte”, spune Brooker. „Ne oferă cu adevărat flexibilitate. Putem folosi cei doi depunători pentru a maximiza capacitatea sau îi putem folosi ca rezervă în cazul în care ceva nu merge bine. Acestea sunt lucrurile mărunte care te fac să treci peste obstacole pentru a-ți îmbunătăți randamentul.”
Cu vitezele crescute ale depunătoarelor, Denver a trecut în 1998 la instalarea unui sistem robotizat mai rapid, de a doua generație, care preia și plasează fursecuri cu o viteză de 1.320 de fursecuri pe minut, în comparație cu 880 de fursecuri pe minut la sistemul mai vechi, instalat inițial în 1988.
Cele 12 brațe robotizate ale noului sistem pot culege și plasa la viteze de 120 pe minut, ceea ce reprezintă aproape dublul vitezei sistemului robotizat „vechi” care are 20 de brațe care lucrează la o rată de 60 până la 75 pe minut. Brooker spune că noul sistem este mai rapid deoarece, cu patru servomotoare, a fost proiectat pentru sarcini utile ușoare la viteze de ciclu mai mari, în timp ce vechiul sistem fusese proiectat pentru sarcini utile mai grele și viteze de ciclu mai mici pentru asamblarea automobilelor și a altor utilaje grele.
Pentru că robotica devine mai sofisticată, mai pricepută și din ce în ce mai accesibilă, perioada de recuperare a investiției a devenit mai scurtă, spune Dave Watson, directorul de inginerie corporativă de la Pepperidge, care a fost inginerul principal și unul dintre arhitecții cheie în demararea fabricii din Denver în urmă cu un deceniu.
Watson notează că prima generație a sistemului robotizat a costat 3,5 milioane de dolari, a dus la economii anuale de 1,1 milioane de dolari în costuri directe cu forța de muncă și compensații pentru muncitori și are o perioadă de recuperare a investiției de 3,9 ani. Aceasta reprezintă o rată internă de rentabilitate (IRR) de 20,2%. Noul sistem a costat 2,0 milioane de dolari, a dus la economii anuale de 1,3 milioane de dolari numai în ceea ce privește forța de muncă directă și are o perioadă de recuperare a investiției de 1,5 ani sau o rată internă de rentabilitate de 41,3%, adaugă Watson.
Capacitatea crescută a determinat Pepperidge Farm să justifice și mai mult o investiție într-un prototip, un sistem robotizat de cupping de fursecuri care preia fursecuri individuale de pe o bandă în mișcare și le încarcă cu pahare de hârtie în mai multe orientări la o rată de 120 de pahare pe minut.
„Dacă nu ai aceste roboți, nu ai putea nici măcar să pui suficienți oameni pe linie pentru a ține pasul cu viteza de producție”, spune Brooker. „Până când nu am atins aceste viteze și nu am dedicat această linie , nu am putut justifica investițiile pe care le-am făcut în ea. Trebuie să o facem să funcționeze în fiecare tură”, ceea ce înseamnă în prezent 15 ture pe săptămână.
Sistemul, care a devenit operațional abia în această vară, dispune de doi roboți cupper care culeg și așează fiecare 660 de fursecuri – sau 100 de pungi – pe minut. Sistemul a costat 3,2 milioane de dolari, va oferi economii anuale de 1,2 milioane de dolari numai în ceea ce privește forța de muncă directă și are o recuperare a investiției în numerar de 3,26 ani sau un IRR de 27,8%.
Ambunătățirile aduse automatizării au permis un sezon de carieră pentru unitatea din Denver în ceea ce privește statisticile, numărul de cutii de produse pentru întreaga fabrică crescând cu 26%, la peste 12 milioane în acest an.
Aceasta este cu aproape 60% mai mult decât cele 7 milioane de cutii de produse produse produse în 1997 și triplu față de cantitatea produsă în primul său an complet de funcționare, în 1992.
În același timp, fabrica și-a redus deșeurile cu 50%, economisind companiei milioane de dolari. Nu este surprinzător să aflăm, așadar, că Denver a câștigat echivalentul premiului MVP atunci când echipa a primit premiul Margaret Rudkin, numit după fondatorul Pepperidge, pentru fabrica anului.
„Am fost destul de norocoși să începem ca o instalație de primă clasă și am investit de-a lungul anilor pentru a o menține la vârf”, spune Moll, care remarcă faptul că Denver a primit anul acesta certificarea ISO 9002. „Vrem să o menținem o instalație de vârf, dar va fi o instalație de vârf și de ultimă generație doar dacă oamenii noștri ne vor duce acolo.”
Ceea ce a impulsionat creșterea Pepperidge Farm în ultimii ani a fost trecerea companiei la o strategie de pictograme, în care compania își pune forța de marketing în spatele celor mai mari și mai bune produse din portofoliul său, inclusiv pâinile Goldfish, Milano și Swirl. Prin creșterea vânzărilor acestor produse, volumele liniei cresc, ceea ce îmbunătățește eficiența producției. Între timp, o parte din banii economisiți prin creșterea eficienței sunt direcționați către programe de marketing și R&D pentru a crea noi ambalaje, pentru a mări bugetele de publicitate sau pentru a lansa noi produse, cum ar fi debutul de succes al Milanos îmbibate cu ciocolată, care vor fi produse în mod sezonier mai târziu în acest an.
Producția funcționează de obicei 24 de ore pe zi, cinci până la șapte zile pe săptămână. Făina în vrac este depozitată în 10 silozuri de 120.000 de lire sterline. Două silozuri de 120.000 de livre dețin zahăr. Făina este transferată în silozuri de utilizare de 20.000-lb. pentru a asigura o scalare precisă și timpi de ciclu mai rapizi. Fabrica are rezervoare de 50.000 de livre pentru untură, sirop de porumb, ulei de canola, ulei amestecat și un rezervor de ciocolată de 80.000 de livre. Șase containere umplute manual conțin ingrediente minore, cum ar fi făina de secară, amidonul și glutenul de grâu. Microingredientele sunt măsurate manual, apoi sunt puse în cărucioare care conțin fiecare câte un lot.
La nivelul mezaninului, camera de control pentru sistemul CIM de la Denver seamănă cu Houston Control, unde computerele centrale de supraveghere supraveghează o rețea de peste 100 de PC-uri cu rezistență industrială conectate prin linii de fibră optică. Fiecare linie are propriul calculator de supraveghere, la fel ca și manipularea și amestecarea ingredientelor. Pepperidge Farm a înlocuit PC/2 IBM 386s PC/2 inițiale cu IBM 486s, care folosesc software și hardware disponibile în general, nu brevetate, ceea ce face ca modernizarea să fie mai accesibilă.
La nivelul mezaninului, pe partea de biscuiți, cinci mixere pentru biscuiți de 1.300 de livre și două mixere pentru biscuiți de 1.500 de livre controlează formularea și timpul de mixare. Toate sunt dotate cu sisteme CO2 pentru a controla temperatura aluatului. După amestecare, loturile cad prin tobogane de 20 de picioare, care sunt ridicate prin fantele de pe podea, la primul nivel.
Pe cele șase linii de biscuiți, trei produc biscuiți acoperiți la bază cu ciocolată sau înveliți în ciocolată. Altele produc fursecuri cu coacere moale, shortbread, pachete de sortimente sau o varietate de fursecuri cu fulgi de ciocolată și alte fursecuri tăiate cu sârmă. Linia 1 produce, de asemenea, snacks-uri Goldfish Graham. Dimensiunile cuptoarelor variază de la 150 la 300 ft. pe liniile de biscuiți.
Poate că cele mai unice sunt liniile Milano. Acolo, după machiaj, fursecurile călătoresc printr-un cuptor de 150 de picioare până la un tunel de răcire de 60 de picioare. Pentru a asigura o răcire adecvată, Pepperidge a folosit un dispozitiv asemănător cu o „cârtiță” de cuptor pentru a măsura temperatura tunelului, viteza aerului și alte variabile. După ce mini-bucătarul aplică învelișul de portocale, mentă sau ciocolată, Milanos călătorește către sistemele robotizate de sandvișuri. Milanos cu umplutură dublă de ciocolată primesc un alt strat de acoperire de la un al doilea bottomer înainte de a fi așezate în sandwich. Deoarece au de două ori mai multă umplutură, Milanos cu umplutură dublă de ciocolată primesc o a doua răcire pentru a se asigura că produsul este sigilat.
În continuare, Milanos se îndreaptă spre cupperul robotizat la o rată de 1.320 pe minut. Folosind un principiu de contra-flux, cinci fursecuri deodată se îndreaptă spre sistemul din față, în timp ce șase cupe deodată sunt denaturate din spate. Un ochi fotografic se asigură că paharele au fost denaturate, în timp ce un al doilea se asigură că prăjitura este acoperită corespunzător. Dacă vede ciocolată neagră, ca în umplutură, și nu vanilie albă, ca în prăjitură, sistemul va presupune că prăjitura nu este sandwichetată. În general, sistemul este programat să umple cupele. Dacă fursecurile nu sunt preluate, sunt transportate până la capăt și reciclate ulterior sau aruncate.
După umplere, cupele umplute fac o buclă de 180° până la împănatoare, care le plasează în pungi, care sunt sigilate, apoi învelite și trimise la depozit.
Pe linia Goldfish, aluatul proaspăt amestecat, crescut cu drojdie, primește o fermentare prelungită înainte de a fi aruncat de la nivelul mezaninului la primul etaj, unde este laminat, decupat și copt. După ce trec prin uscătorul cu radiofrecvență, care reduce la jumătate umiditatea produsului până la nivelul potrivit, Goldfish călătoresc printr-un condimentator și un nou acumulator de dimensiuni mai mari, care a fost instalat atunci când capacitatea liniei a fost dublată.
Din acumulator, Goldfish se îndreaptă spre transportoare cu găleți către unul dintre numeroasele dispozitive de scalare, care plasează greutatea exactă a produsului în ambalajul de mai jos. După ce sunt sigilate, pungile umplute de Goldfish călătoresc într-un singur rând către ambalatoarele de cutii.
Pe linie, senzori sofisticați monitorizează meticulos culoarea, umiditatea, înălțimea și cantitatea de ulei sau sare. Personalul de control al calității prelevează în mod obișnuit mostre de pe linie pentru notare și testare.
În vastul depozit, angajații despart produsele de pe benzile transportoare în funcție de depozit. În fiecare zi, aproximativ 40 de remorci de tractor sunt umplute la Denver, a cărui operațiune de biscuiți deservește 120 de depozite din mijlocul Atlanticului și New England. În mod obișnuit, depozitul deține un stoc de biscuiți și biscuiți pentru o săptămână.
Streamlining changeovers sunt două domenii pe care compania încearcă să le îmbunătățească în ceea ce privește biscuiții. Anterior, Denver efectua schimbările după fiecare schimb de 8 ore. Acum, fabrica le face în mijlocul schimbului „pentru a ne reduce inventarul aproape de zero”, spune Moll.
„Învățăm de la partea de panificație cum să schimbăm din mers”, explică Moll. „Scopul nostru este să ducem acest proces de gândire și pe partea de biscuiți.”
Dezvoltarea de noi produse este un alt domeniu în care Pepperidge Farm și fabrica sa din Denver se străduiesc să eficientizeze. Anterior, în mod normal, era nevoie de 4-6 luni pentru a introduce un produs nou. În cadrul unui nou program numit „Project Lightening”, compania dorește să treacă de la conceptul ideii la producție în două luni.
Aceste provocări de a reduce costurile, de a spori calitatea, de a îmbunătăți producția și de a crește siguranța, împreună cu cele 20 de standarde stricte ale certificării ISO 9002, l-au determinat pe Moll să reorganizeze structura de management a fabricii. Astăzi, pentru a supraveghea producția, Denver are trei manageri de produs – câte unul pentru panificație, biscuiți și biscuiți – care raportează directorului de operațiuni, William Livingstone. Pentru a supraveghea ingredientele care intră și produsele care ies, managerii de planificare, recepție, depozitare și expediere raportează managerului lanțului de aprovizionare, Stephen Lieb.
„O parte din motivul pentru schimbările sistematice pe care le-am făcut se datorează creșterii companiei de-a lungul anilor”, spune Moll. „Și cum a trebuit să aducem oameni noi, avem nevoie de un sistem puternic pentru a produce în mod constant produse care să se ridice la standardele companiei noastre.”
Întrebat ce ar face diferit dacă ar avea șansa de a reconstrui din nou instalația din Denver de la zero, Moll răspunde: „Nu cred că este vorba despre ce am fi făcut diferit. Am făcut o treabă bună. Este o fabrică minunată. Sarcina noastră este – pe măsură ce tehnologia se schimbă – să îmbunătățim ceea ce avem aici și să o facem mai bună.”
Cu un astfel de mandat, se poate spune cu siguranță că pentru Pepperidge Farm „nu există niciodată o zi obișnuită” în Denver, Pa.
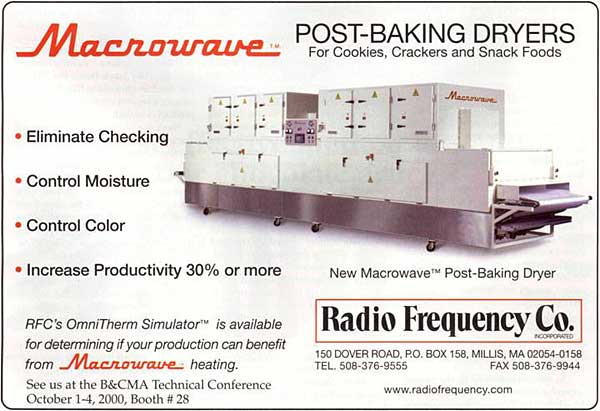
.