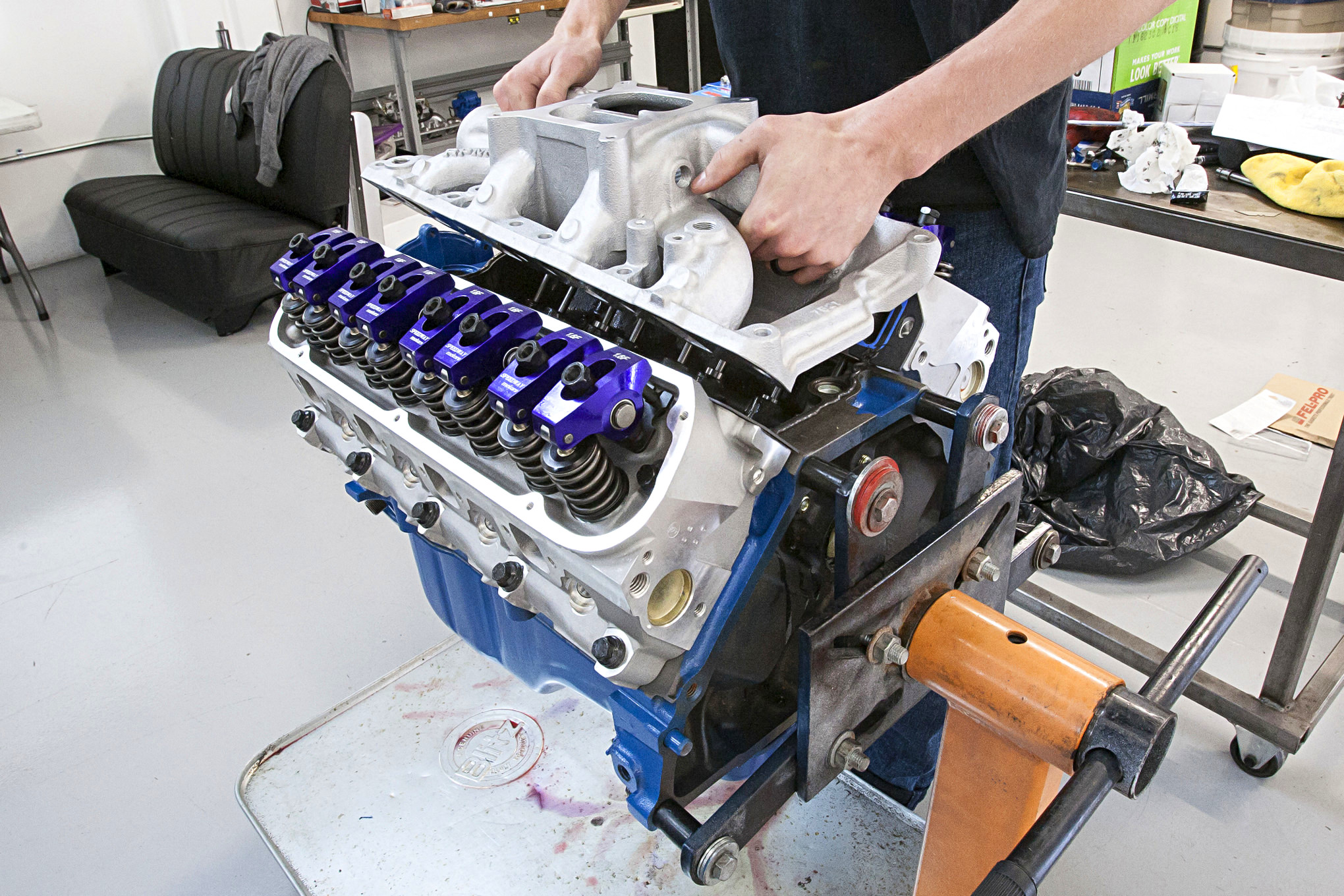
Ob Sie Teil 1 dieses wallet-freundlichen Small-Block-Umbaus mitverfolgt haben oder nicht, Sie werden Teil 2 nicht verpassen wollen. Diesmal geht es darum, einem handelsüblichen 1971er 302er Small-Block eine gesunde Dosis Leistung zu verpassen. Wir nehmen das, was ein durchschnittlicher Umbau sein könnte, und geben ihm einen kleinen Aftermarket-Schwung, indem wir das serienmäßige Top-End zugunsten einiger Goodies, die wir von Speedway Motors abgeholt haben, über Bord werfen.
Mit einem Satz preiswerter Aluminiumköpfe von Flo-Tek als Katalysator haben wir eine Handvoll anderer Top-End-Teile in der Hoffnung, den kleinen 302 in die Nähe von 350 PS zu bringen, ausgearbeitet. Diese Zahl mag in den Tagen der 1.000-PS-Internet-Helden nicht beeindruckend klingen, aber wenn Sie sich erinnern, kamen die Small-Block-Ford-Motoren aus den frühen 1970er Jahren nicht weit über die 200-PS-Marke hinaus. Wenn Sie also wie wir von einem 302er gezogen wurden, wissen Sie, dass Sie eine Leistungssteigerung von über 100 PS spüren werden.
Was war also der Angriffsplan, werden Sie sich fragen? Nun, die bereits erwähnten Flo-Tek-Köpfe waren es, die uns zum Nachdenken brachten. Vormontiert (Ventilsitze, Ventile, Ventilfedern und Ventilteller) kosten diese Dinger um die 400 Dollar pro Stück, so dass wir mit 800 Dollar für ein Paar Hochleistungs-Aluköpfe einen guten Start hatten. Nun ging es darum, die richtige Auswahl an unterstützenden Modifikationen zu treffen, angefangen mit dem Ansaugkrümmer. Dies war wahrscheinlich die einfachste Entscheidung, und da wir eine straßentaugliche Leistung anstrebten, war ein Edelbrock Performer RPM Air-Gap eine Selbstverständlichkeit. Wir haben immer wieder gesehen, dass diese Ansaugkrümmer eine solide Leistung am oberen Ende des Leistungsbandes erbringen, ohne das Drehmoment im unteren Bereich und die Fahrbarkeit zu beeinträchtigen.
Als nächstes stand die Wahl der Nockenwelle an. Wir wollten etwas, das die Vorteile der strömungsstärkeren Zylinderköpfe und des Ansaugkrümmers nutzt, aber auch nicht zu viel im unteren Bereich einbüßt. Außerdem wollten wir es billig und einfach halten, also entschieden wir uns für einen hydraulischen Tassenstößel. Von Speedway Motors erhielten wir eine Nockenwelle mit einer Einlass- und Auslassdauer von 219/233 bei 0,050 und einem Hub von .477/.510 mit 110 Grad Nockenabstand. Um den Ventiltrieb zu vervollständigen, entschieden wir uns für einen Satz 1,6:1-Rollenkipphebel von Speedway Motors mit einem 3/8-Zoll-Stehbolzen, passend zu den Flo-Tek-Köpfen.
Um Kraftstoff und Luft in den Motor zu bekommen, hätten wir uns für eine EFI-Anlage entscheiden können, aber da das Wort „Budget“ im Titel dieser Geschichte vorkommt, beschlossen wir, es einfach und erschwinglich zu halten. Daher haben wir uns für einen Holley 650-cfm Double Pumper entschieden. Zur Verschönerung haben wir uns für einen Satz schwarzer Aluminium-Ventildeckel von Speedway Motors mit Rippen und einen passenden ovalen 12-Zoll-Luftfilter entschieden. Und nein, wir haben den Zündfunken nicht vergessen; unsere 302 war bereits mit einem HEI All-in-One Verteiler ausgestattet, der gut funktionierte, also haben wir ihn nur gereinigt und einen Satz MSD Street Fire Zündkerzenkabel und neue Zündkerzen besorgt.
Das Endergebnis war nicht nur schön anzusehen (ja, wir sind ein bisschen voreingenommen), sondern es erfüllte auch unsere Erwartungen in Bezug auf die Leistung. Lesen Sie weiter, um zu sehen, wie wir von einem nackten Block und einem Haufen Teile zu einer 350-PS-Mühle kamen, die sofort einsatzbereit ist.
1. Als Erstes überprüfen wir das Spiel der Kurbelwellenzapfen, indem wir unsere Clevite-Hauptlager in die Hauptlagerzapfen und -deckel einbauen. Denken Sie daran, die Lager Kerbe an Kerbe einzubauen und sie fest einzupressen, um sicherzustellen, dass jedes Ende des Lagers bündig sitzt.
2. Nachdem wir alle Hauptschrauben mit dem vorgeschriebenen Anzugsmoment angezogen haben, überprüfen wir das Spiel zwischen Kurbelwellenzapfen und Lager mit einer Messuhr und einer Messschraube. Wenn das Spiel zu eng oder zu locker ist, ist es besser, das jetzt herauszufinden, als nur die Finger zu kreuzen und zu beten, dass alles gut geht, wenn man den Motor zum ersten Mal zündet.
3. Als Nächstes haben wir die zweiteilige hintere Hauptdichtung mit der Nut nach innen eingebaut und nicht aushärtende Luftfahrtdichtmasse auf der Rückseite und den oberen Kanten verwendet. Ob Sie die Dichtung bündig oder versetzt einbauen, bleibt Ihnen überlassen, aber manche behaupten, dass eine Seite höher als die andere liegt, um das Öl besser zurückzuhalten.
4. Wenn Sie sich selbst nicht wirklich vertrauen, ist es am besten, ein zweites Paar Hände zu haben, wenn Sie die Kurbelwelle einbauen – vergessen Sie nicht, alle Lagerflächen gründlich mit Motormontageöl zu bedecken. Es ist auch eine gute Idee, etwas Schmiermittel auf die Innenseite der hinteren Hauptdichtung aufzutragen, damit sie nicht an der Kurbelwelle hängen bleibt.
5. Bringen Sie alle Hauptkappen an und ziehen Sie sie dann mit dem vorgeschriebenen Drehmoment an, wobei Sie in der Mitte beginnen und sich nach außen vorarbeiten.
6. Dies hätte auch früher oder später geschehen können, aber als Nächstes haben wir die Kernstopfen mit nicht aushärtendem Luftfahrtdichtungsmittel an den Kanten eingedreht.
7. Dann überprüften wir mit einer Messuhr und einer magnetischen Basis das Kurbelwellenspiel, indem wir einen Schraubendreher zwischen den Hauptkappen und den Gegengewichten ansetzten, um die Kurbelwelle nach vorne und hinten zu drücken.
8. Bevor wir die Ringe auf unsere Wiseco Pro Tru Street-Schmiedekolben montierten, gingen wir nach alter Schule vor und benutzten eine Feile in einem Schraubstock, um jeden Ring zu spalten. Technischer Tipp: Ein Ringfeilwerkzeug macht das Leben viel einfacher.
9. Nachdem die Ringe eingelassen und auf den Kolben montiert waren, bereiteten wir die Pleuelstangen vor, indem wir die Pleuellager einfügten und einschmierten. Dann benutzten wir ARP Ultra-Torque Fastener Assembly Lubricant für die Stangenbolzen.
10. Die Verwendung eines maßgeschneiderten 4,030-Zoll-ARP-Kolbenringkompressors mit konischem Querschnitt ist der Königsweg, um die Kolben zu installieren, ohne einen Ring zu quetschen.
11. Wir zogen dann alle Stangenschrauben mit dem vorgeschriebenen Anzugsmoment an, bevor wir die Nockenwelle mit Nockenwellenschmiermittel bestrichen und sie einführten. Ein längerer Bolzen mit demselben Gewinde und Durchmesser wie der Nockenwellenbolzen kann verwendet werden, um die Nockenwelle an Ort und Stelle zu hebeln, wenn es schwierig wird.
12. Der Steuersatz war der nächste. Hier kommt es darauf an, dass die beiden kleinen Punkte – einer auf dem Kurbelwellenrad und einer auf dem Nockenwellenrad – auf der Innenseite aufeinander ausgerichtet sind. Wenn Sie sich der Nockenwelleneinstellung absolut sicher sein wollen, verwenden Sie ein Gradrad, um sie einzustellen, aber die Methode „Ausrichten der Punkte“ ist in den meisten Fällen in Ordnung, besonders bei Markennockenwellen.
13. Dann installierten wir einen Kopf, um die Stößelstangenlänge zu überprüfen, indem wir einen roten Marker auf dem Ventilschaft verwendeten. Nachdem wir zwei Stößel, Stößelstangen und Kipphebel eingebaut und den Motor ein paar Mal von Hand gedreht hatten, hinterließen die Kipphebelspitzen die hier zu sehenden Markierungen. Noch weiter unten wären die Stößelstangen zu lang gewesen, noch weiter oben wären sie zu kurz gewesen.
14. Bevor wir den Kopf einbauten und den Motor ein paar Mal durchdrehten, klebten wir etwas Lehm auf, um das Spiel zwischen Kolben und Ventilen zu prüfen. Mit einem Tiefenmessgerät stellten wir fest, dass zwischen den Ventilen und den Ventilentlastungen im Kolben meilenweit Platz war.
15. Bevor wir den Rest der Stößel einbauten, schmierten wir sie mit dem gleichen Schmiermittel ein, mit dem auch die Nockenwelle montiert wurde. Andernfalls könnten die Stößel und die Nockenwelle während des Einfahrens des Motors ernsthaft beschädigt werden, insbesondere bei Nocken mit flachen Stößeln.
16. Wir montierten die Flo-Tek-Aluminiumköpfe mit ARP-Kopfschrauben, und nachdem die Stößel, Stößelstangen und Rollenkipphebel an ihrem Platz waren, stellten wir das Ventilspiel ein. Wir drehten den Polylock von Hand herunter, bis er kaum noch Widerstand fand. Dann, nach einer weiteren halben Umdrehung, sperrten wir es ab.
17. Wir drehten den Motor wieder um und bauten die serienmäßige Ölpumpe und den Ölabnehmer ein, indem wir Schraubensicherung auf die Schrauben auftrugen und diese mit dem vorgeschriebenen Drehmoment anzogen.
18. Dann haben wir die Kurbelwellenabdichtung eingebaut. Wie die Kernstopfen kann auch die Kurbelwellendichtung mit einer großen Stecknuss desselben Durchmessers eingebaut werden.
19. Als Nächstes wurden die Ölwanne und der Steuergehäusedeckel montiert und mit dem vorgeschriebenen Drehmoment angezogen.
20. Dann kam der Edelbrock RPM Air-Gap Ansaugkrümmer dran. Vielleicht haben Sie auch bemerkt, dass ARP uns einen Satz seiner Edelstahl-Zubehörschrauben geschickt hat, um alles zusammenzuhalten.
21. Beim Einbau der Speedway Motors-Ventilabdeckungen haben wir die Oberseite der Fel-Pro-Dichtung mit einem nicht aushärtenden Dichtmittel versehen, damit die Dichtung später, wenn wir die Abdeckungen vom Kopf entfernen wollen, nur an den Ventilabdeckungen haften bleibt.
22. Als Nächstes kam die Ausgleichswelle dran. Wie die Ölwanne, der Steuergehäusedeckel, die Riemenscheiben und andere Serienteile haben wir den originalen Balancer vor dem Einbau gereinigt und lackiert.
23. Dann installierten wir das Thermostat, das Thermostatgehäuse und die Wasserpumpe an der Vorderseite des 302.
24. Das Ende nahte, als wir die Riemenscheiben und Zubehörhalterungen montierten, eine Aufgabe, die noch einfacher war als sonst, da wir keine Klimaanlage oder Servolenkung hatten.
25. Die letzten Schritte umfassten die Installation des neuen Holley 650-cfm Double Pumper, des alten HEI-Verteilers, der Street Fire-Zündkerzen und des zum Ventildeckel passenden Speedway Motors-Luftfilters.
26. Soweit es den Geldbeutel betrifft, sieht dieser leistungsorientierte Small-Block-Ford ziemlich gut aus, wenn wir das selbst sagen.
27. Er sieht nicht nur gut aus, sondern ist auch sehr leistungsfähig. Nachdem wir ihn bei der Westech Performance Group in Mira Loma, Kalifornien, auf dem Prüfstand getestet hatten, erreichte unser kleiner 302er 348 Spitzen-PS bei 6.000 U/min und 347 lb-ft Drehmoment bei 4.100 U/min – technisch gesehen zwar keine 350 PS, aber wir beanspruchen den Sieg trotzdem für uns.